Bio-Brick Labs voted most exciting innovation at CCA Annual Conference
The CONtact mentorship program, launched in 2018 by CCA in partnership with the National Research Council, helps innovators and entrepreneurs in construction to connect with industry experts. CCA, together with industry experts, have mentored nearly 30 mentees over the last five years.
At CCA’s 2023 CCA Annual Conference, three CONtact mentees were selected to present their innovations to conference delegates and industry experts at an Innovator’s Pitch session. This year’s experts were John Bockstael, CEO, Bockstael Construction; Quentin Huillery, Chief Operating Officer, Constructors (Civil Mining and Infrastructure), Ledcor; and Harold Reinders, President and CEO, Maple Reinders Group Ltd.
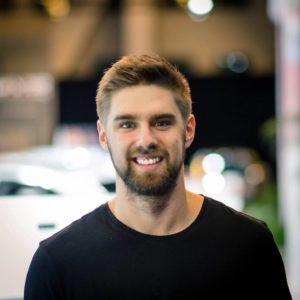
Laurent Blanchet
Co-Founder, Biolift Technologies
LinkedIn
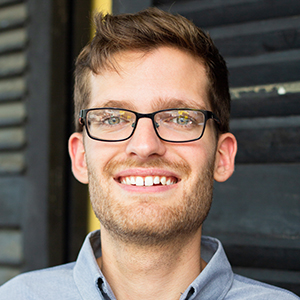
Jeff Carmichael
Co-Founder, Qualomate
LinkedIn
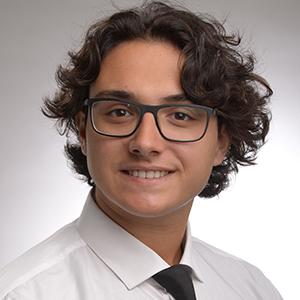
Adrian Simone
Co-Founder, Bio-Brick Labs
LinkedIn
Following a presentation by each mentee and questions by the panel of industry experts, the audience voted on the innovation they were most excited to see implemented in the industry.
Adrian Simone of Bio-Brick Labs, a bio-tech company focused on the research, development, and manufacturing of environmentally sustainable masonry units was selected the winner of The Innovator’s Pitch. The bio-brick, made using only two ingredients (bacteria and aggregate), solidifies at room temperature, eliminating carbon emissions in the solidification process.
CCA caught up with Adrian after the conference to discuss his innovation and his experience with the CONtact mentorship program.
CCA: How did Bio-Bricks come to be? Why this particular innovation?
Adrian Simone: Bio-Brick Labs came from the realization that while the way we build and the equipment we build with has changed significantly, the materials we use have not. The pollutant exposure for people who make the materials and the environments in which they are made are the same as what they were 50 years ago. High heats and the reliance on fuels to make them has made the material manufacturing industry responsible for 22 per cent of global emissions. We wanted to create a material that didn’t emit any dangerous fumes or smoke, and didn’t require heat to cure. This goal went hand-in-hand with both improving the conditions for manufacturers and limiting environmental effects.
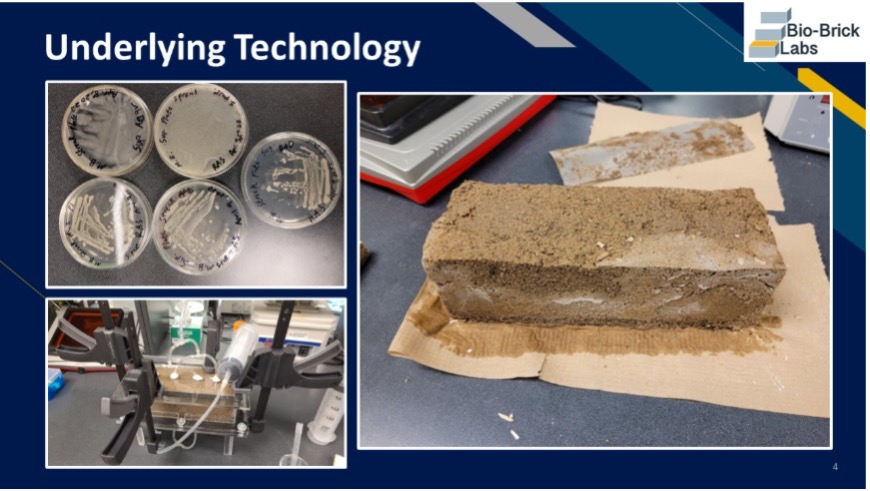
We looked to nature for our solution. We use stone to build, and have since the beginning of time, but what natural processes can create this stone? By using a naturally occurring bacterial process we can create a brick with the same properties, feel, and installation as what we use now, but with none of the emissions. It is made at room temperature with no need for kilns or ovens, and solidifies in the same time as clay-fired masonry.
Another goal for us was to cut down on the required transportation from where the material is made to where it is used. As gas prices continue to increase, bulky material like masonry will start having its price affected by the transportation requirements. Our process can be scaled to fit into a portable unit such as a shipping container. This will allow for the transportation of the material to be cut down and allow for localized manufacturing.
CCA: You participated in the CCA CONtact mentorship program and was chosen to pitch your solution to industry experts at CCA’s conference. How have these experiences helped you? And how will this shape your work moving forward?
Adrian Simone: I joined the CCA CONtact mentorship program because I wanted to see if embodied carbon was an issue in the industry that people cared about and wanted a solution to. It gave me the opportunity to ask numerous industry professionals how they see the problem and what needs they have for the solution. All these questions were answered. And we will use the advice that we received at the conference in our future testing. Making sure that it looks the same, focusing on the procedures surrounding portable manufacturing, and ensuring that all the testing we do is identical to the testing requirements current materials go through.
Most of all, the industry experts got us thinking about how we can change the material to benefit the final user. Being able to change our molds so that the bricks bite mortar better, making bricks lighter so they are more efficient to install, etc. – changes that can make the work on-site easier and faster for construction companies.
CCA: Although you touched on this in your presentation at the Annual Conference, what do you feel is the biggest benefit to Bio-Bricks, and why should the construction industry look at this new product over existing masonry?
Adrian Simone: The Bio-Brick allows companies that want to go in a more sustainable route, a feasible and competitive solution. Current green supplies can be expensive with mark-ups as high as 32 per cent, and have been found to increase construction times by 11 per cent. These increases in money and time do not make them practical for most projects, but we’ve found that a lot of construction companies want to start moving in a sustainable direction. This will allow those companies to start lowering their embodied carbon while still remaining on budget and on time.
When compared to existing masonry, it’s more a question of why not. Competitively priced against most traditional clay-fired or concrete masonry options, a lower manufacturing time, identical installation process, and more customizability in the visual properties your product can take. We can replicate the look of any material we use as an aggregate allowing for versatility and the ability to match existing material. On top of all this we’re carbon neutral in our manufacturing, which no other brick supplier can offer.
The CONtact mentorship program connects innovators with industry experts. Over the past five years, numerous industry experts have lent their time and expertise to mentor the program’s innovators. Quentin Huillery, Chief Operating Officer, Constructors (Civil Mining and Infrastructure) of Ledcor, offers his thoughts on the winning Innovator’s Pitch and his reasons for supporting the CONtact mentorship program.
What excited you the most about Bio-Brick Labs innovation?
A focus on sustainability and a drive towards carbon reduction is a critical initiative for our planet, and often the construction industry is criticized for not doing enough in this regard. The young entrepreneurs that are behind this exciting new product are doing a fantastic job of changing this narrative.
Why do you consider it important to be part of the CONtact mentorship program?
Unfortunately, our construction industry has lagged behind many other industries with regard to innovation and advancements that offer sustainability and execution efficiencies. Assisting those that are focused on correcting this is rewarding because our industry depends on the technology these innovators are advancing.
As we look to encourage new innovators to apply to the CONtact program in the future, what areas would you like to see more innovation?
As the available labour force continues to be strained within the construction industry, I think it is critical to continue to explore innovations that offer execution efficiencies
Learn how you can become a CONtact mentor or mentee ↗